Cylindrical rollers, smooth and uniform like tiny cylinders, are essential rolling elements in many machines. They are primarily used where flat surfaces need to make contact, providing low friction in one direction and high load-bearing capacity. This makes them ideal for applications that require precision and the ability to support heavy loads.
As machines operate and generate friction and heat, cylindrical rollers reduce wear and tear by rolling between moving parts. This allows the components to glide smoothly, rather than sliding and causing damage, which ultimately extends the machine's lifespan and enhances performance.
As machines operate and generate friction and heat, cylindrical rollers reduce wear and tear by rolling between moving parts. This allows the components to glide smoothly, rather than sliding and causing damage, which ultimately extends the machine's lifespan and enhances performance.
Smooth, uniform, and shaped like tiny cylinders, cylindrical rollers are a type of rolling element that is vital to many machines. They are mainly used where the contact surface is flat, offering low friction in one direction and high load-carrying capacity, making them perfect for applications requiring precision and support for heavy loads.
Because of the friction and heat generated during operation, cylinder rollers help prevent this wear and tear by rolling between the moving parts, allowing the parts to glide smoothly rather than sliding and breaking down over time. This increases machine longevity and improves machine performance.
Benefits in Industrial Applications
Raw Material Arrival and Storage: High-quality raw materials are chosen and carefully stored to maintain their integrity and quality.
Rigorous Cutting: The raw materials are cut into exact pieces, customized to the exact specifications for the rollers.
Hammering: The sliced components are rigidly formed by hammering, which creates the roller's base.
Heat Treatment: To achieve optimal performance, the rollers go through a specific heat treatment process that increases their strength and durability.
Precision Grinding: To attain the ideal dimensions and a faultless surface finish, the rollers are finely ground, guaranteeing consistency.
Polishing: Every roller is flawlessly polished, producing a high-quality, elegant finish.
Comprehensive Visual Examination: Every roller undergoes a comprehensive visual examination to guarantee that only the highest-caliber products proceed.
Grading: Each roller is tested for quality and compliance with strict requirements before being scrupulously ranked.
Secure Packaging: The completed rollers are packaged safely to guarantee their undamaged state throughout transportation.
Dispatch: After this accurate process, the rollers are carefully shipped out, prepared to provide our esteemed clients with outstanding performance.
Maximum load capacity: Compared to balls, cylindrical rollers can support higher radial loads. They are capable of both high speeds and heavy radiators.
Minimal friction: Cylindrical rollers can rotate at high speeds due to the low friction between the rollers and ring ribs.
High load-carrying capacity: The high load-bearing capacity of cylindrical rollers is the primary factor that makes them the industry standard. The line contact formed between the rollers and raceways puts heavy radial loads on the bearings.
Effortless installation: Cylindrical rollers are easy to install and less likely to break because they are flush and slim inside the housing.
Resistant to contamination: Rolling elements used in abrasive environments should be resistant to dirt, dust, and other outside contaminants. This can be achieved in rollers by installing shields and seals to prevent contamination from entering their internal components.
Efficiency in Terms of Costs In the long run, cylindrical rollers are economical. Quality cylindrical rollers may cost more initially, but they are more than offset by the savings on maintenance, downtime, and replacement costs.
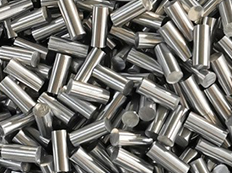


Steel is the most commonly used material for balls due to its hardness and resistance, making it suitable for various applications. The performance of steel balls, including hardness, durability, and load capacity, depends on the type of steel and its treatment.
Steel balls are vital for smooth, efficient motion in industrial machinery. Since 2018, SKP Bearing Industries Limited has been producing high-quality steel balls, ranging from 0.6 mm to 16.00 mm, using advanced machinery and rigorous quality control. Our reputation for reliability is backed by our state-of-the-art testing equipment, including roundness testers, hardness testers, diameter control instruments, and roughness testers.
Steel balls are vital for smooth, efficient motion in industrial machinery. Since 2018, SKP Bearing Industries Limited has been producing high-quality steel balls, ranging from 0.6 mm to 16.00 mm, using advanced machinery and rigorous quality control. Our reputation for reliability is backed by our state-of-the-art testing equipment, including roundness testers, hardness testers, diameter control instruments, and roughness testers.
FAQs
Answer: Cylindrical rollers are employed in machine tools, conveyor systems, and automotive transmissions, among other industrial applications where they are required to sustain radial loads.
Answer: In comparison to other roller types, cylindrical rollers have a larger length-to-diameter ratio that enables them to support larger radial loads while still having a compact design.
Answer: If installed and lubricated properly, cylindrical rollers can run at high speeds, which makes them appropriate for applications requiring quick motion.
Answer: It is true that cylindrical rollers are adaptable and flexible enough to handle loads in a variety of industrial applications, both radial and axial.
Answer: When choosing cylindrical rollers, keep things like load capacity, speed, operating environment, and space constraints in mind. Our expert team can advise you on the best option for your particular requirements.